Open-Web Trusses,
optimize over compromise.
Pound for pound, RedBuilt Open-Web trusses are among the strongest structural members produced. Often a solution for exceptionally long spans, they’re still a powerful choice for all types of commercial applications.
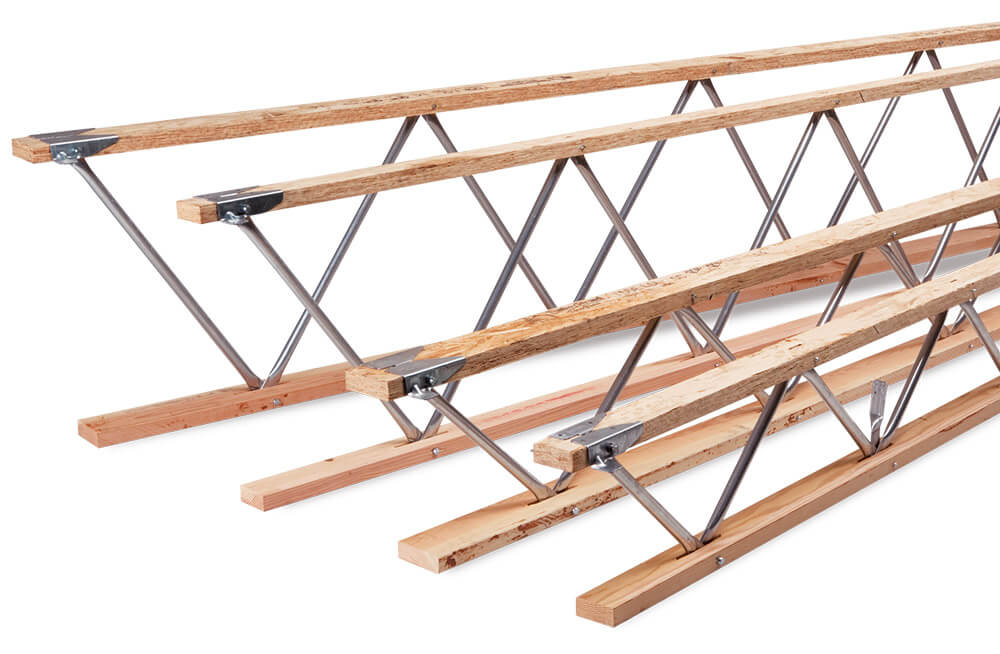
RedBuilt Open-Web Trusses offer a variety of solutions for a broad range of challenges. Whether your project is for retail or office space, a school, multi-family apartments, condos, assisted living facilities, hotels and motels, warehouses, you name it, an open floor plan is often a primary requirement. These strong, light and highly customizable Open-Web Trusses add design flexibility for owners/developers to create market-specific and relevant spaces.
Available Profiles:

Parallel Chord

Tapered

Pitched

Radius Pitched
*Not available in Red-M, or Red-H

Bow String
*Not available in Red-M, or Red-H

Barrel
*Not available in Red-M, or Red-H

Pitched Top/Radius Bottom
*Not available in Red-M, or Red-H
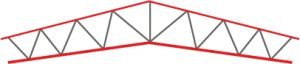
Scissor

Compound Barrel
*Not available in Red-M, or Red-H

Lenticular
*Not available in Red-M, or Red-H
TOP & BOTTOM CHORDS | WEBS
(minimum yield of 45,000 psi per ASTM A500, Grade C) |
WEIGHT | AVAILABLE DEPTHS
(at wall) |
SPECIAL CONSIDERATIONS | |
---|---|---|---|---|---|
Red-L™ | 1-1⁄2” x 3-1⁄2” flatwise
MSR lumber |
1” and 1 1⁄8” diam. tubular steel members varying in gauge and diameter according to requirements. | 3.75 to 4.25 lbs/ft | 14”– 50”
(Max. pitched ridge depth = 50”) |
Lightweight and efficient |
Red-W™ | 1-1⁄2” x 4-3⁄4” flatwise
MSR lumber |
1” and 1 1⁄8” diam. tubular steel members varying in gauge and diameter according to requirements. | 4.5 to 5.25 lbs/ft | 14”– 50”
(Max. pitched ridge depth = 50”) |
A slightly heavier duty truss for mid-range spans |
Red-S™ | Double 1-1⁄2” x 2.3” edgewise
RedLam™ LVL |
1 1⁄4” and 1 1/2” diam. tubular steel members varying in gauge and diameter according to requirements. | 4.75 to 5.75 lbs/ft | 16”– 60”
(Max. pitched ridge depth = 84”) |
Offers strength, efficiency and economy for large open areas such as in schools, offices and warehouses |
Red-M™ | Double 1-1⁄2” x 3-1⁄2” edgewise
MSR lumber |
Up to 2” diam. tubular steel members varying in gauge and diameter according to requirements. | 8 to 9 lbs/ft | 20”– 60”
(Max. pitched ridge depth = 72”) |
Can easily accommodate heavy loads and long spans—ideal for offices, warehouses, auditoriums and shopping centers |
Red-H™ | Double 1-1⁄2” x 5-1⁄2” edgewise
MSR lumber (Upgrade may be available as RedLam LVL) |
Up to 2” diam. tubular steel members varying in gauge and diameter according to requirements. | 10 to 12 lbs/ft | 24”– 72”
(Max. pitched ridge depth = 114”) |
Can easily accommodate heavy loads and long spans—ideal for offices, warehouses, auditoriums and shopping centers |
RED-OW-88 Sound Test with lightweight concrete & 5/8″ Sheetrock on Resilient channels
79kb DWG Download DWG
111kb PDF Download PDF
RED-OW-87 Sound Transmission Test (STC 48) 2 Layers Sheathing
75kb DWG Download DWG
115kb PDF Download PDF
RED-OW-86 Sound Transmission Test (STC 48) Homasote Decking
75kb DWG Download DWG
118kb PDF Download PDF
RED-OW-88 Sound Test with 5/8″ Sheetrock on Resilient channels
75kb DWG Download DWG
121kb PDF Download PDF
Wall Fire Assembly (Design 5)
75kb DWG Download DWG
Wall Fire Assembly (Design 4)
77kb DWG Download DWG
Wall Fire Assembly (Design 3)
76kb DWG Download DWG
Wall Fire Assembly (Design 2)
75kb DWG Download DWG
Wall Fire Assembly (Design 1)
76kb DWG Download DWG
Two-Hour Assembly (Fire Assembly G)
83kb DWG Download DWG
One-Hour Assembly (Fire Assembly E)
79kb DWG Download DWG
One-Hour Assembly (Fire Assembly D)
80kb DWG Download DWG
One-Hour Assembly (Fire Assembly C)
79kb DWG Download DWG
One-Hour Assembly (Fire Assembly B)
76kb DWG Download DWG
One-Hour Assembly (Fire Assembly A)
84kb DWG Download DWG
Fire Sprinkler EQ 02 – for forces parallel or perpendicular to open-web trusses
90kb DWG Download DWG
Fire Sprinkler EQ 01 – For forces perpendicular to open-web trusses
101kb DWG Download DWG
Fire Sprinkler 11 – Red-L™, Red-W™, Red-S™ Trusses
95kb DWG Download DWG
Fire Sprinkler 10 – Red-L™, Red-W™, Red-S™ Trusses
93kb DWG Download DWG
Fire Sprinkler 09 – Red-M™ and Red-H™ Trusses
114kb DWG Download DWG
Fire Sprinkler 08 – Red-M™ and Red-H™ Trusses
106kb DWG Download DWG
Fire Sprinkler 07 – Red-L™, Red-W™, Red-S™ Trusses
112kb DWG Download DWG
Fire Sprinkler 06 – for all Open-Web Trusses
105kb DWG Download DWG
Fire Sprinkler 05 – for all Open-Web Trusses
90kb DWG Download DWG
Fire Sprinkler 04 – for Red-L™, Red-W™, Red-M™, Red-H™ Trusses
102kb DWG Download DWG
Fire Sprinkler 03 – for all Open-Web Trusses
96kb DWG Download DWG
Fire Sprinkler 02 – for Red-L™ Trusses
98kb DWG Download DWG
Fire Sprinkler Details 01 – for all Open-Web Trusses
133kb DWG Download DWG
Flush Mount Wood Ledger Cap 1
104kb DWG Download DWG
Flush Mount Wood Beam Cap 2
103kb DWG Download DWG
Flush Mount Wood Beam Cap 1
103kb DWG Download DWG
Flush Mount Steel Ledger Cap 1
98kb DWG Download DWG
Flush Mount Steel Ledger
98kb DWG Download DWG
Flush Mount Steel Beam Cap 2
84kb DWG Download DWG
Flush Mount Steel Beam Cap 1
84kb DWG Download DWG
Flush Mount Steel Beam
85kb DWG Download DWG
76 – 3½” Wide Chords or Cap Plates on Double Cord Trusses
71kb DWG Download DWG
117kb PDF Download PDF
73 Double Chord Open-Web Truss with Continuous Panel Joint
66kb DWG Download DWG
36kb PDF Download PDF
71 Double Chord Open-Web Truss with SIP or Tectum Panels
140kb DWG Download DWG
4kb PDF Download PDF
RedBuilt Open-Web Truss with Cap Plate (Swan Lumber Cap Plate and LSL Cap Plate)
85kb DWG Download DWG
160kb PDF Download PDF
Top Chord Bearing Flush-Mount Bearing Clip (Dropped and Non-Dropped)
71kb DWG Download DWG
92kb PDF Download PDF
Top Chord Bearing Red-S™ Truss Butting with Red-L™ and Red-W™ Trusses
72kb DWG Download DWG
104kb PDF Download PDF
RedBuilt Open-Web Truss Design Guide
7667kb PDF Updated Apr 2021 Download PDF
Total Support Brochure
57317kb PDF Updated Mar 2020 Download PDF
Red-S™ Heavy S-Clip Lateral Bearing Clip with Extended Base Plate (TB-105)
217kb PDF Updated Oct 2021 Download PDF
Red-S™ Heavy S-Clip Bearing Clip (TB-104)
207kb PDF Updated Oct 2021 Download PDF
Long Span Installation Guide (TB-301)
2970kb PDF Updated Nov 2016 Download PDF
Fire Facts Guide
2801kb PDF Updated Jun 2016 Download PDF
Open-Web Trusses (for Canada)
1409kb PDF Download PDF
Sprinkler System Installation Guide
5773kb PDF Updated Jan 2016 Download PDF
RedBuilt Open-Web Truss Design Guide
7667kb PDF Updated Apr 2021 Download PDF
Environmental Product Declaration (EPD) – RedBuilt Open-Web Trusses
1434kb PDF Updated Dec 2021 Download PDF
Red-S™ Heavy S-Clip Lateral Bearing Clip with Extended Base Plate (TB-105)
217kb PDF Updated Oct 2021 Download PDF
Red-S™ Heavy S-Clip Bearing Clip (TB-104)
207kb PDF Updated Oct 2021 Download PDF
PFS-TECO Listed Fire-Rated Assemblies
No files found
Intertek Listed Fire-Rated Assemblies
No files found
Parapet Assemblies (TB-400)
656kb PDF Updated Jan 2022 Download PDF
RedBuilt™ Open Web Truss Specification – North America
13kb DOCX Download DOCX
RedSpec™ Product Sizing Software Brochure
369kb PDF Updated Aug 2014 Download PDF
Fire Facts Guide
2801kb PDF Updated Jun 2016 Download PDF
FloorChoice™ Floor Performance
2061kb PDF Updated Jun 2010 Download PDF
Open-Web Trusses (for Canada)
1409kb PDF Download PDF
Sprinkler System Installation Guide
5773kb PDF Updated Jan 2016 Download PDF
Environmental Product Declaration (EPD) – RedBuilt Open-Web Trusses
1434kb PDF Updated Dec 2021 Download PDF
Health Product Declaration (HPD) – RedBuilt Open-Web Trusses
357kb PDF Updated Mar 2024 Download PDF
Wood Dust (SDS)
406kb PDF Download PDF
Green Building Solutions Q&A
151kb PDF Updated May 2024 Download PDF
Red-S™ Heavy S-Clip Lateral Bearing Clip with Extended Base Plate (TB-105)
217kb PDF Updated Oct 2021 Download PDF
Red-S™ Heavy S-Clip Bearing Clip (TB-104)
207kb PDF Updated Oct 2021 Download PDF
Lateral Capacity of Open-Web Truss Bearing Clips (TB-100)
253kb PDF Updated Mar 2023 Download PDF
Secondary Treatments (TB-300)
123kb PDF Updated Mar 2016 Download PDF
Long Span Installation Guide (TB-301)
2970kb PDF Updated Nov 2016 Download PDF
Parapet Assemblies (TB-400)
656kb PDF Updated Jan 2022 Download PDF
PFS-TECO Listed Fire-Rated Assemblies
No files found
Intertek Listed Fire-Rated Assemblies
No files found
ICC-ES Report ESR-1774 with LABC Supplement: Open Web Trusses
No files found
PFS-TECO Listed Fire-Rated Assemblies
No files found
Intertek Listed Fire-Rated Assemblies
No files found
Fire Facts Guide
2801kb PDF Updated Jun 2016 Download PDF
Sprinkler System Installation Guide
5773kb PDF Updated Jan 2016 Download PDF
ICC-ES Report ESR-1774 with LABC Supplement: Open Web Trusses
No files found
Fabricator Certificate – Miami-Dade County, Open-Web Trusses
253kb PDF Updated Aug 2024 Download PDF
Fabricator Certificate – City of Los Angeles, Open-Web Trusses
410kb PDF Updated Jul 2025 Download PDF
Fabricator Certificate – City of Houston, Open-Web Trusses, RedLam LVL & Red-I Joists
514kb PDF Updated Nov 2024 Download PDF
Fabricator Certificate – City of Seattle, Open-Web Trusses
219kb PDF Updated Jun 2025 Download PDF
RedBuilt™ Product Warranty Letter
316kb PDF Updated Mar 2020 Download PDF
Product Warranty Certificate
155kb PDF Updated Mar 2020 Download PDF
Long Span Installation Guide (TB-301)
2970kb PDF Updated Nov 2016 Download PDF
Open-Web Truss Installation Information (Metric)
551kb PDF Updated Jan 2022 Download PDF
Open-Web Truss Installation Information
1183kb PDF Updated Dec 2023 Download PDF
Open-Web Truss Installation Information (Spanish)
1013kb PDF Updated Jan 2022 Download PDF
Sprinkler System Installation Guide
5773kb PDF Updated Jan 2016 Download PDF
RedSpec™ Product Sizing Software Brochure
369kb PDF Updated Aug 2014 Download PDF
FloorChoice™ Floor Performance
2061kb PDF Updated Jun 2010 Download PDF
Wood Dust (SDS)
406kb PDF Download PDF
RED-H™ Pitched Profile
2300kb RFA Updated Feb 2021 Download RFA
RED-H™ Tapered Profile
1832kb RFA Updated Feb 2021 Download RFA
RED-L™ Pitched Profile
2424kb RFA Updated Feb 2021 Download RFA
RED-L™ Radius Pitched Profile
1236kb RFA Updated Jul 2019 Download RFA
RED-L™ Tapered Profile
1856kb RFA Updated Feb 2021 Download RFA
RED-L™ and RED-W™ Parallel Profile
692kb RFA Updated Feb 2021 Download RFA
RED-M™ Pitched Profile
2300kb RFA Updated Feb 2021 Download RFA
RED-M™ Tapered Profile
1832kb RFA Updated Feb 2021 Download RFA
RED-S™ Pitched Profile
2300kb RFA Updated Feb 2021 Download RFA
RED-S™ Radius Pitched
1224kb RFA Updated Jul 2019 Download RFA
RED-S™ Tapered Profile
1828kb RFA Updated Feb 2021 Download RFA
RED-S™, RED-M™ and RED-H™ Parallel Profile
704kb RFA Updated Feb 2021 Download RFA
RED-W™ Pitched Profile
2300kb RFA Updated Feb 2021 Download RFA
RED-W™ Radius Pitched Profile
1288kb RFA Updated Jul 2019 Download RFA
RED-W™ Tapered Profile
1916kb RFA Updated Feb 2021 Download RFA